Fahrzeugunterböden aus Naturfasern und Recycling-Kunststoffen
Gemeinsam mit Industriepartnern haben Forschende des Fraunhofer WKI einen Fahrzeugunterboden aus Naturfasern sowie recycelten Kunststoffen für den Automobilbau entwickelt. Das Bauteil erfüllt die hohen technischen Anforderungen im Unterbodenbereich und könnte zukünftig herkömmliche Leichtbau-Fahrzeugunterböden ersetzen. Mit dieser Entwicklung wird die Klima- und Umweltbilanz über den gesamten Produktlebenszyklus optimiert. Der Fokus des Fraunhofer WKI lag auf der Materialentwicklung für den Spritzguss sowie auf der Hydrophobierung von Flachs- und Hanffasern für naturfaserverstärkte Mischfaservliese.
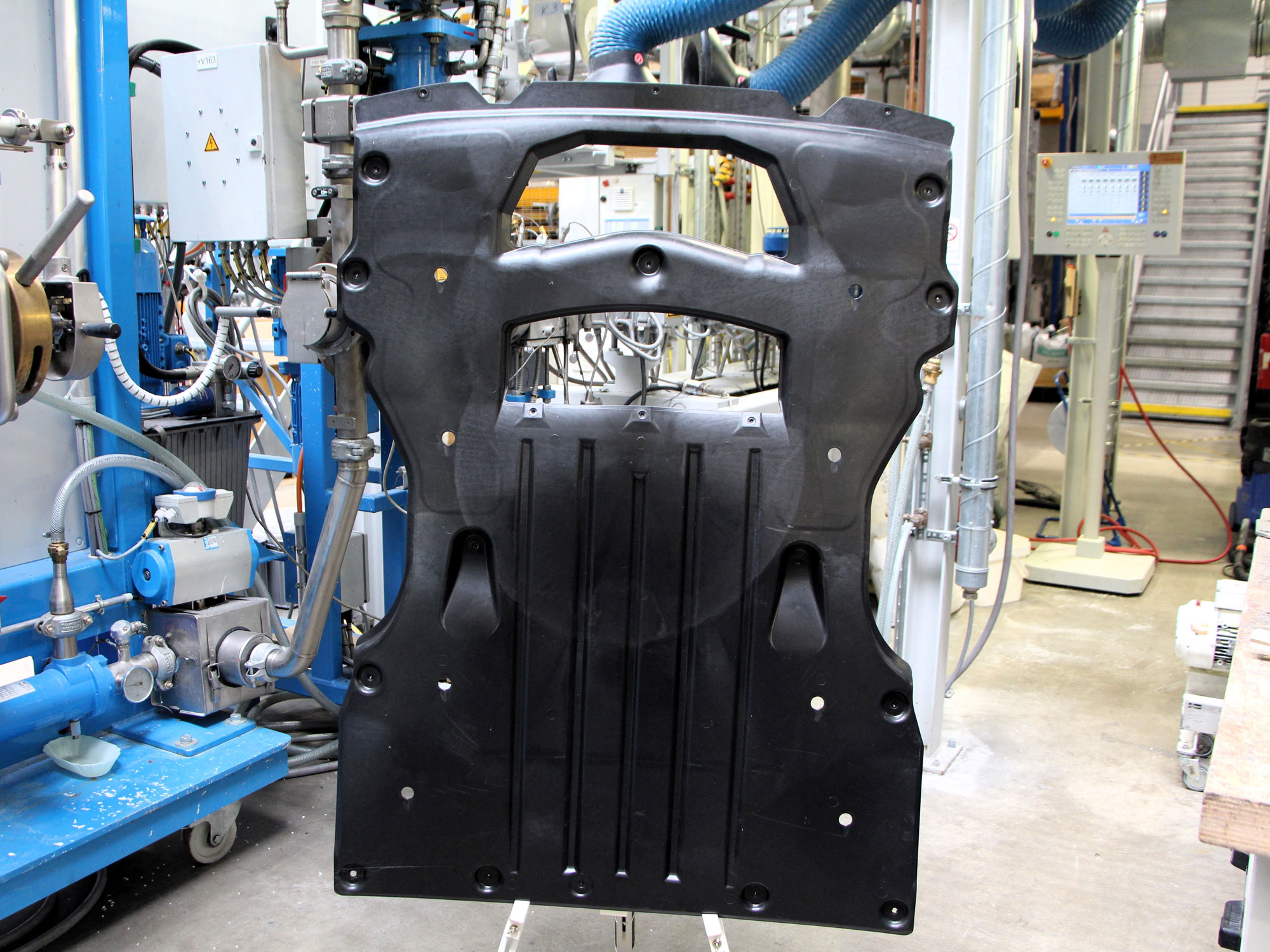
Den Projektpartnern Fraunhofer WKI, Thüringisches Institut für Textil- und Kunststofftechnik (TITK), Röchling Automotive SE & Co. KG, BBP Kunststoffwerk Marbach Baier GmbH und Audi AG ist es gelungen, ein nachhaltiges Gesamtkonzept für Fahrzeugunterböden zu entwickeln. Damit haben die Forschenden eine anspruchsvolle Bauteilgruppe mit hohem Kunststoffanteil für den Einsatz von Naturmaterialien erschlossen. Bisher wurden naturfaserverstärkte Kunststoffe im Automobil hauptsächlich für Verkleidungsteile ohne nennenswerte mechanische Aufgaben eingesetzt. Strukturelle Bauteile wie Fahrzeugunterböden sind jedoch enormen Belastungen ausgesetzt und stellen hohe Anforderungen an das Biege- und Crashverhalten des Materials. In modernen Leichtbau-Fahrzeugkonzepten kommen daher Hochleistungswerkstoffe aus glasfaserverstärkten Kunststoffen zum Einsatz.
Das Projektteam konnte die Glasfasern durch Naturmaterialien wie Flachs-, Hanf- und Cellulosefasern ersetzen und Unterbodenbauteile mit einem Naturfaseranteil von bis zu 45 Prozent realisieren. Im Bereich der Polymere wurde vollständig auf Polypropylen-Neuware verzichtet und ausschließlich Rezyklate eingesetzt. Alle mit dieser Materialumstellung verbundenen Herausforderungen, sowohl die geringeren mechanischen Ausgangseigenschaften der Werkstoffe als auch die zeitlich eingeschränkten Verarbeitungsfenster, konnten durch geschickte Compoundkombinationen gelöst werden.
Am Fraunhofer WKI wurden Materialien für den Spritzguss entwickelt. »Naturfaser-Spritzguss-Compounds sind bisher vor allem durch Festigkeits- und Steifigkeitssteigerungen gegenüber unverstärkten Polymeren bekannt. Bei der Entwicklung im Fahrzeugunterboden ist es darüber hinaus gelungen, durch eine innovative Kombination von ausgewählten Post-Consumer-Rezyklaten (PCR) als Matrix und Naturfasern unterschiedlicher Reinheitsgrade die hohen Anforderungen an die Kaltschlagzähigkeit zu erfüllen, ohne dabei die geforderte Steifigkeit und Festigkeit einzubüßen«, erklärt Moritz Micke-Camuz, Projektleiter am Fraunhofer WKI.
Im Rahmen der Entwicklung wurden am TITK und bei Röchling erstmals Faserverbundbauteile aus naturfaserverstärktem Mischfaservlies (Lightweight-Reinforced-Thermoplastic, LWRT) realisiert. Das entwickelte Produkt erfüllt nicht nur die mechanischen Anforderungen. Es widersteht insbesondere auch den Herausforderungen, die durch die feuchte Einsatzumgebung hervorgerufen werden. Zur Hydrophobierung von Flachs- und Hanffasern für LWRT-Bauteile wurde am Fraunhofer WKI ein kontinuierliches Furfurylierungsverfahren entwickelt. Durch die Furfurylierung kann die Feuchtigkeitsaufnahme um bis zu 35 Prozent reduziert werden, ohne die Biegefestigkeit der späteren Bauteile zu beeinträchtigen. Das furfurylierte Fasermaterial lässt sich zudem problemlos auf einer Vliesanlage weiterverarbeiten
Die gefertigten Prototypenbauteile wurden anschließend sowohl auf Komponentenebene als auch im Fahrversuch intensiv getestet. Dazu dienten unter anderem die Fahrzeuge der neuen »Premium Platform Electric« (PPE) des VW-Konzerns. Im Rahmen der Serienerprobung konnten bereits Langzeiterfahrungen gesammelt werden. Das erfreuliche Ergebnis dieser Tests: Die neu entwickelten Bioverbundwerkstoffe erfüllen alle Standardanforderungen an Unterbodenbauteile und erweisen sich als serientauglich. Weder der Einsatz von Naturfasern noch von (Post-Consumer-)Rezyklaten führt zu einer signifikanten Beeinträchtigung der Eigenschaften.
Ein wesentlicher Vorteil der Innovation liegt auch in der deutlich verbesserten CO2-Bilanz: Im Vergleich zur Serie können 10,5 Kilogramm Neuware (PP/Glasfaser) durch 4,2 Kilogramm Naturfasern und 6,3 Kilogramm Post-Consumer-Rezyklat ersetzt werden. Dadurch konnten die CO2-Emissionen während der Produktion, der Nutzung und des Produktlebens um bis zu 40 Prozent reduziert werden.
Im Rahmen des Entwicklungsprojektes wurde ein innovatives, ganzheitliches Gesamtkonzept für Fahrzeugunterböden inklusive Recycling mit kaskadischer Wiederverwendung der Komponenten entwickelt. Aus technischer Sicht können Fahrzeugunterböden zukünftig vollständig aus dem neuen, hochleistungsfähigen Bio-Leichtbau-Material hergestellt werden.
Letzte Änderung: